
Lean Transformation Consultancy
Bengaluru
Business Management Consultancy Services
![]() |
---|
Always making the things better
We take responsibility to keep enhancing our capability to meet evolving need of the customer.
Process
​
-
Understand customer's problem
-
Gemba to understand current state
-
Explore the Management's target state
-
Build people capabilities to transform
People
​
-
Take challenges to its logical end
-
Continuous self-development
-
​Accept the other's struggle as own
-
Strive to achieve the true potential
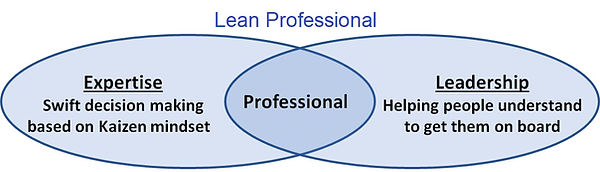
Lean management has spawned the quality movement, the excellence movement, and countless re-engineered and reverse-engineering theories. Its need has been felt as long as there is a will to survive all times and perform better, and the need felt more so than now, as we enter an era of intentional transition.
​
Toyota has performed so well since its crisis in 1950 due to its lean thinking. Excellent companies around the globe have come and gone. Some perform well from time to time, year to year, then go on the skids for a while. Many have gone out of business.
What is Lean Management?
Lean Management is to enhance value for customers with less resources expended.
​
The idea behind is to discover a better way of doing things. People are key to discover this better way, by understanding how the work is currently being done, unearthing the problems in current way of doing the work, developing solutions to the problems and transforming the work.
Lean management is a series of practices that develops people to understand and own their problems and align resources to achieve the purpose of the organization. It engages everyone in designing processes to continuously solve problems, improve performance, and achieve purpose while consuming the least resources.
​
Lean Management can be characterized as a continuous series of controlled experiments. It encourages people for continuous experimentation. It governs the way people do their work, the way they interact with one another, the way production or service value streams are constructed, and the way people learn and improve. Every activity, linkages, and value creation path is designed to sense and surface problems rather than hiding the problem. Together, people find innovative solutions to the problems. As the processes and system matures, the standards are raised to create the problem.
​
" No problem is the biggest problem."
​
People have a natural ability to change things for better and sense things instinctively which machines can never do. We are encouraged to see the facts by personally seeing, feeling and interpreting the current situation at the place of work, to discover the current problem, and develop creative and better solutions. Finding problems requires developing an awareness of problems even in situations those look perfectly normal - seeing the waste like; Why are we waiting? Why do we need to do this rework? Why is the product accumulating? How do we make the work easier to do?
​
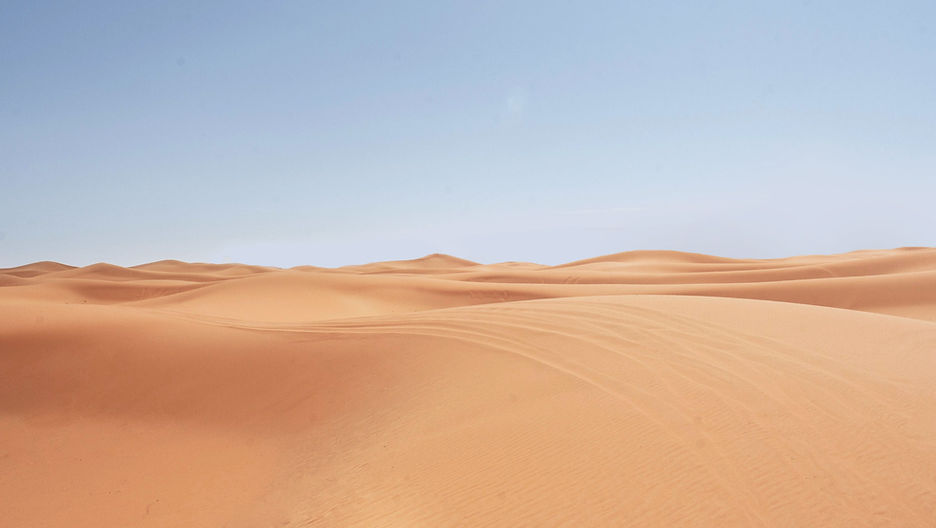